In the bustling world of construction and manufacturing, coil sheets have emerged as an essential material, prized for their versatility and efficiency. Their widespread application across various industries is a testament to their reliability and adaptability. Professionals within these sectors recognize the indispensable role that high-quality coil sheets play in the production process, continually seeking the most advanced and durable options to enhance product longevity and performance.
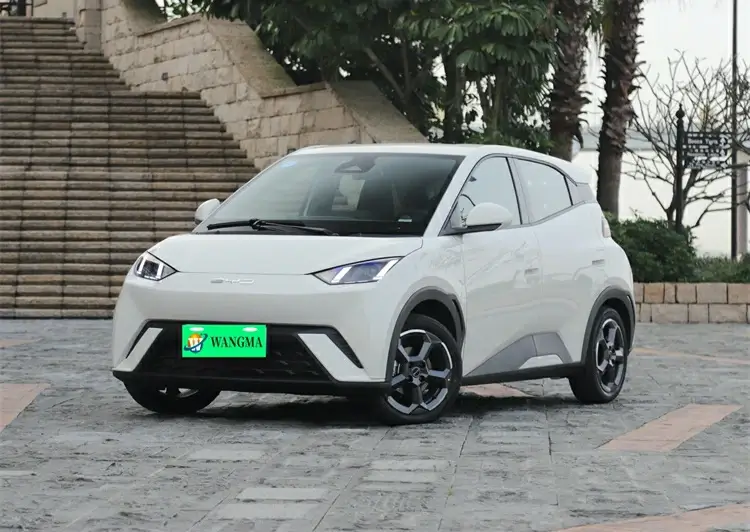
One of the distinct advantages of coil sheets is their availability in multiple materials such as steel, aluminum, and copper. Each type caters to specific industrial needs,
offering unique benefits. Steel coil sheets, for instance, are celebrated for their strength and durability, making them the material of choice for constructing sturdy structures and frameworks. On the other hand, aluminum coil sheets are lightweight, corrosion-resistant, and highly malleable, making them ideal for projects that require flexibility without compromising integrity. Copper coil sheets, known for their excellent thermal and electrical conductivity, find their niche in electrical applications and HVAC systems.
Professionals dealing with coil sheets understand the complexities involved in selecting the right type and grade. A deep dive into the specifications of these materials often reveals insights crucial for optimizing their application. For example, the grade of steel used in a coil sheet can significantly affect the strength and flexibility of the end product. Similarly, the temper of aluminum sheets can dictate their malleability and resistance to wear and tear. This knowledge underscore the importance of partnering with suppliers that emphasize comprehensive material intelligence and quality assurance.
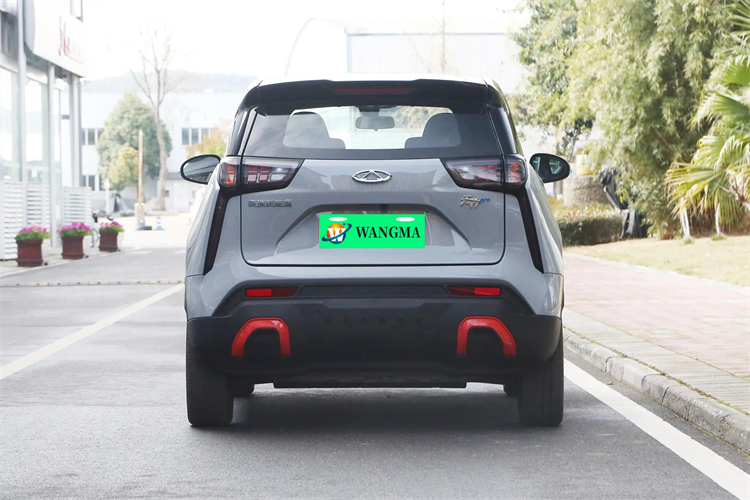
Beyond material choice, the production process of coil sheets is a key contributor to their performance. Leading manufacturers employ state-of-the-art rolling and coating techniques to ensure that each coil sheet meets stringent quality standards. Cold rolling processes impart superior surface finish and enhanced mechanical properties, while hot rolling provides toughness and strength. Additionally, protective coatings such as galvanization or anodizing enhance durability, extending the life span of coil sheets even in harsh environments.
coil sheets
Companies investing in top-tier coil sheets can expect substantial returns in terms of product dependability and customer satisfaction. A tangible sense of trust and authority is conveyed through the provision of consistent, high-performing materials, thereby solidifying industry reputation and client relationships. Testimonials and case studies from satisfied customers further bolster the credibility and authority of coil sheet providers, establishing them as leaders in the marketplace.
Moreover, continuous innovation in the coil sheet sector keeps professionals abreast of the latest advancements. Cutting-edge research emphasizes the development of eco-friendly materials, such as recycled or more sustainable alloys, which meet both performance and environmental standards. As the industry shifts towards green manufacturing, companies that adopt and promote these innovations not only gain a competitive edge but also contribute significantly to global sustainability efforts.
In conclusion, coil sheets represent an integral component in the toolkit of construction and manufacturing industries. The confluence of material expertise, advanced manufacturing processes, and a commitment to sustainability ensures that businesses that prioritize high-quality coil sheets are positioned for success. By consistently delivering materials that exceed industry standards, these businesses fortify their role as authoritative, trustworthy partners in a demanding and dynamic market.