Maximizing the utility of corrugated steel sheets comes down to understanding one crucial variable thickness. Selecting the appropriate thickness is more than just a technical decision; it requires a blend of practical experience, specialized knowledge, and a firm grounding in material science. To ensure durability, functionality, and cost-effectiveness, one must delve deep into the factors influencing the ideal thickness of corrugated steel sheets for diverse applications.

Corrugated steel sheets have become synonymous with robust construction due to their high strength-to-weight ratio, excellent durability, and versatile usability. The thickness of these sheets determines their load-bearing capacity, resistance to environmental variables, and overall lifetime.
From historical experience, structures exposed to rigorous environmental conditions, such as coastal or industrial areas, require steel sheets with greater thickness. This is crucial in enhancing resistance to corrosion and mechanical stress. Selecting thinner variants may lead to premature wear and structural instability, undermining both safety and investment.
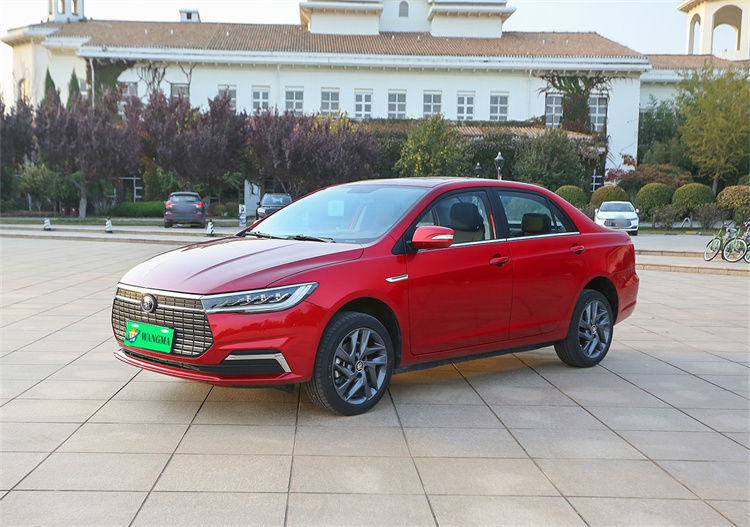
Specialized expertise in engineering principles reveals that the thickness of corrugated steel sheets significantly influences their mechanical properties. For roofing applications, architects often recommend a baseline thickness that aligns with regional climatic conditions. In areas prone to heavy snowfall or high winds, a thicker steel sheet ensures better performance by providing superior structural support. Conversely, regions with milder climates can afford to use thinner sheets, optimizing costs without sacrificing integrity.
Authoritative standards, such as those from ASTM and ISO, provide meticulous guidelines on the thickness of steel sheets for specific purposes. These standards epitomize years of empirical research and testing, offering a reliable benchmark for both manufacturing and application. Compliance with these standards ensures that structures not only achieve longevity but also conform to safety protocols, thereby minimizing liability risks.
corrugated steel sheet thickness
Trustworthiness in selecting the appropriate thickness emerges from both brand reliability and product certification. Engaging with manufacturers that demonstrate transparency and accreditation from recognized bodies promises quality. Trust is built through consistent performance; manufacturers with a robust portfolio of successful projects stand as testimonies to their product's reliability.
Advanced technologies and manufacturing processes have facilitated the production of variable thickness steel sheets with precise specification adherence. Cold rolling, for instance, has been pivotal in achieving enhanced surface finish and controlled thickness distribution, maximizing the sheet's application potential without incurring excessive material costs.
Innovative applications beyond traditional construction further necessitate careful consideration of thickness. For instance, in modern architecture, where aesthetics intertwine with structural components, corrugated steel sheets serve as both facade and support, demanding optimal thickness for visual appeal and foundational strength. Similarly, in renewable energy installations, such as solar panel frames, the thickness directly affects installation ease, durability, and overall efficiency.
In conclusion, determining the right thickness for corrugated steel sheets is not merely a matter of technical specification but a comprehensive approach bridging experience, expert analysis, authoritative guidelines, and trustworthiness. Whether for residential buildings, industrial complexes, or avant-garde architectural projects, the prudent selection of corrugated steel sheet thickness significantly impacts performance, safety, and long-term economic viability, robustly supporting modern construction needs.