Galvanized iron has long been a staple in various industries due to its versatility, strength, and corrosion resistance. Understanding the density of galvanized iron not only helps in determining the weight of different products but also plays a crucial role in manufacturing and logistics processes, influencing decisions ranging from material selection to cost calculations.
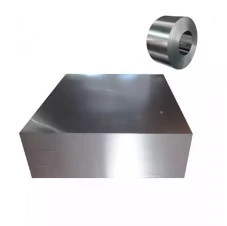
The density of a material, essentially its mass per unit volume, is a key factor in determining its strength and durability. For galvanized iron, density is more than just a number; it serves as an indicator of the additional protective coating of zinc that ensures the longevity and robustness of the iron underneath. Typically,
galvanized iron has an average density of around 7.8 grams per cubic centimeter. This density is slightly higher than that of plain iron due to the layer of zinc added during the galvanization process.
Firstly, let's delve into the galvanization technique, which involves coating iron with a protective layer of zinc. This is accomplished through two primary processes hot-dip galvanizing and electro-galvanizing. Hot-dip galvanizing immerses the iron in molten zinc, forming a thick, robust layer. Conversely, electro-galvanizing employs an electric current to coat the iron with a thinner, more precise layer of zinc. Both methods affect the density, albeit marginally, due to the variable thickness of the zinc coating.
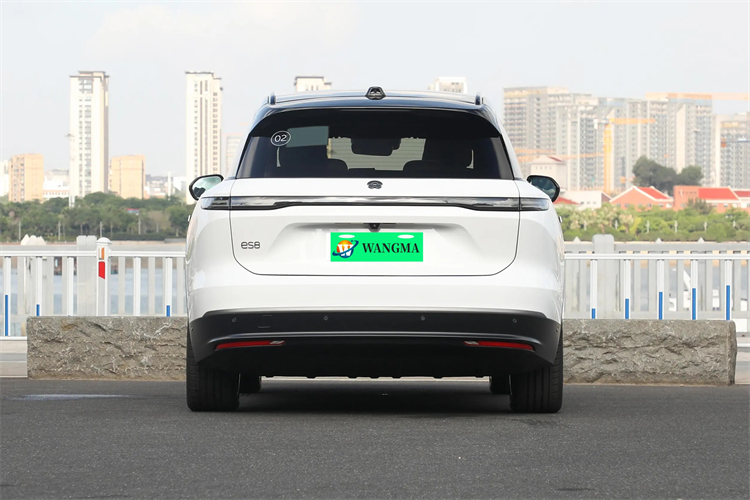
One aspect of expertise lies in recognizing how the density of galvanized iron impacts its application. Products made from this material are widely used in environments susceptible to rust and corrosion, such as coastal constructions and outdoor installations. For example, in maritime settings, where exposure to saline water poses a significant risk of rust, selecting galvanized iron can dramatically extend the lifespan of structures and components.
From an engineering perspective, understanding the density of galvanized iron is instrumental in calculating load-bearing capacities, particularly in construction and infrastructure development. Engineers often rely on precise density measurements to ensure their designs can withstand expected loads and environmental conditions without compromising structural integrity.
density of galvanized iron
The authority of galvanized iron in the market also stems from its trustworthiness in critical applications. In sectors like automotive manufacturing, its density provides balance between weight and strength, crucial for producing safe yet efficient vehicles. Furthermore, product developers often cite the material's consistent density as a reason for its reliability in mass production, ensuring uniform quality across large production runs.
Professionals involved in supply chain management also benefit from their knowledge of galvanized iron’s density. Accurate density calculations facilitate efficient transportation logistics by enabling better predictions of shipping costs, load management, and storage requirements. By knowing the exact density, companies can prevent overloading transport vessels, thus averting potential logistical bottlenecks and additional expenses.
The environmental implications of using galvanized iron should not be overlooked. Its durability reduces the need for frequent replacements, thereby conserving resources and minimizing industrial waste. Additionally, due to the density-driven efficacy of its zinc coating, products made with galvanized iron are less likely to degrade, lowering the environmental footprint over their lifecycle.
In summary, while the density of galvanized iron might seem like a straightforward metric at first glance, its implications are far-reaching. From ensuring the longevity and stability of structures, informing manufacturing processes, enhancing logistical planning, to promoting sustainability, the density of galvanized iron holds the key to numerous industrial benefits. Mastery of this seemingly simple trait can thus significantly boost operational efficiencies and economic gains across various sectors, reinforcing its enduring relevance in modern engineering and manufacturing.