Galvanized iron caps have emerged as quintessential components in various industries, driven by their exceptional durability, corrosion resistance, and versatility. These attributes make them indispensable across applications ranging from construction to manufacturing, providing solutions that are both practical and economically viable.
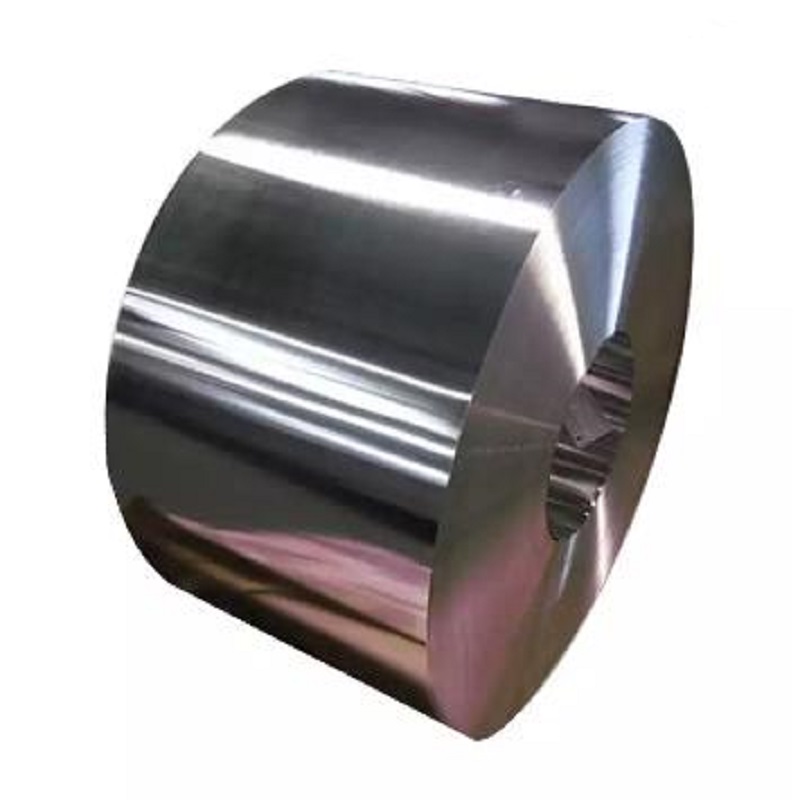
Galvanization, the process of applying a protective zinc coating to iron, serves as a defense mechanism against rust and environmental corrosive elements. This enhancement is particularly crucial for applications where metallic components are exposed to harsh weather conditions, ensuring longevity and optimal functionality. For instance, in coastal areas where salty air prevails, galvanized iron caps perform exceedingly well, protecting structural fastenings and mechanical linkages from potential deterioration.
In the construction industry, galvanized iron caps are paramount, often utilized to shield the ends of tubing and piping structures in both commercial and residential projects. The fundamental objective here is not only to resist corrosion but to enhance the aesthetic value of the architectural application. Given the weight they carry in maintaining structural integrity, any compromise on their quality can lead to significant financial losses and safety hazards, reaffirming their role as an investment rather than an expense.
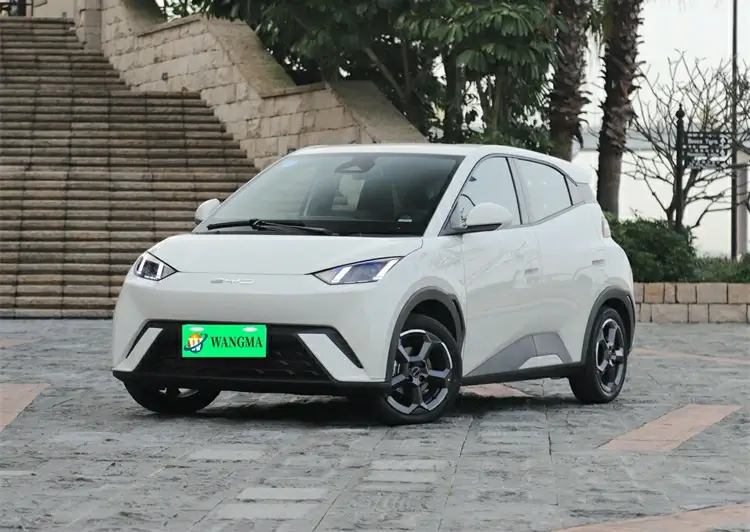
Moreover, experts in metal fabrication underscore the importance of these caps in the assembly of equipment where precision is non-negotiable. Whether it pertains to mechanical assemblies in automotive sectors or the meticulous configurations within aerospace engineering, the deployment of galvanized iron ensures that every joint and terminal is robust, thereby reducing maintenance frequency and overall lifecycle costs.
From a commercial perspective, the rise in demand for galvanized iron caps has stimulated innovations in their designs. Manufacturers are now focusing on adaptive technologies, enhancing fitting accuracy and easy installation features, thereby streamlining operations across various industrial applications. This continuous development is a testament to the material's resilience and the industry's commitment to sustainability through prolonged service life of components.
galvanized iron caps
The environmental implications of using galvanized iron caps cannot be ignored. Zinc, the key element in the galvanization process, is naturally abundant and recyclable, aligning with global efforts towards sustainable development. Industries leveraging these materials contribute to a reduced carbon footprint by prolonging the lifespan of their structures and frequently utilizing recycled metals in production cycles.
As industry experts affirm, the credibility of galvanized products is reinforced through rigorous testing and adherence to international standards. Organizations that prioritize quality assurance through certifications and quality control protocols reinforce the trustworthiness of galvanized iron caps. This focus on quality is crucial, as it assures stakeholders of both performance and commitment to safety standards.
Historically, the use of iron has transitioned through myriad innovations, yet galvanization remains one of the most significant advancements, consistently proving its worth. As technology progresses, so too does the potential for improving galvanization techniques, thus expanding the capabilities and applications of these vital components.
In conclusion, galvanized iron caps embody the intersection of durability, efficiency, and sustainability. For engineers, architects, and plant managers, the advantages they offer extend beyond mere functionality—they signify a proactive approach to risk management and environmental stewardship.
The enduring appeal and necessity of galvanized iron in contemporary industry are anchored in its proven track record of excellence and reliability.