Galvanized iron and mild steel are two prominent materials widely used in the construction and manufacturing sectors due to their distinct properties and advantages. Understanding the differences and applications of these materials is crucial for professionals looking to optimize their projects in terms of durability, cost-efficiency, and performance.
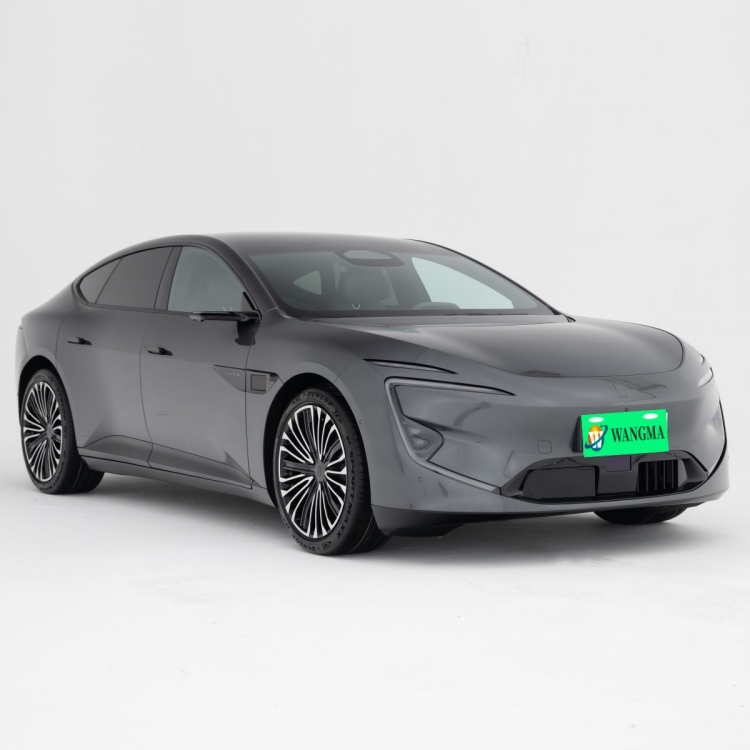
Galvanized iron is essentially steel coated with a layer of zinc through a process known as galvanization. This protective layer is the key to its renown; it offers superb resistance to corrosion, significantly extending the material's life, particularly in environments exposed to moisture and harsh weather conditions. As a result, galvanized iron is an ideal choice for outdoor structures such as roofing, fencing, and pipelines, where durability against rust is paramount.
On the other hand, mild steel, known for its lower carbon content compared to other forms of steel, provides flexibility and weldability, making it a versatile option in various engineering applications. Despite being more susceptible to corrosion than galvanized iron, mild steel can be readily shaped into different forms, offering a level of ductility that facilitates intricate construction designs and manufacturing processes.

Professionals often face a decision-making process when choosing between these two materials. While galvanized iron provides unparalleled corrosion resistance, its brittleness can be a constraint in applications requiring extensive flexibility. For example, in projects where extensive bending and shaping are necessary, mild steel's pliability and ease of fabrication make it preferable despite the need for additional protective measures against corrosion, such as painting or coating.
Economic factors also play a significant role in material selection. Galvanization adds to the overall cost due to the extensive processing involved, and this can impact budget-sensitive projects. Meanwhile, the abundance and manufacturability of mild steel often translate to a more cost-effective option, particularly in applications where exposure to the elements is minimal or where post-fabrication treatments are feasible within project budgets.
galvanized iron mild steel
The decision between galvanized iron and mild steel also involves consideration of environmental conditions. In marine environments, for instance, the high exposure to saline and moisture means that galvanized iron's superior rust resistance is worth the additional costs it incurs. Conversely, for indoor structural work where moisture is not a significant concern, mild steel's affordability and ease of manipulation make it the practical choice.
Application experience shows that for long-term investments where maintenance cost and longevity are critical, such as in infrastructural developments, galvanized iron is the superior choice. In contrast, mild steel's flexibility makes it ideal for temporary structures and components where frequent replacements are anticipated or design complexity demands greater structural adaptability.
In industrial applications, mild steel proves advantageous due to its machinability. It can be easily drilled, cut, or welded into complex components, which is essential for the custom manufacturing of machinery or components subject to substantial wear-and-tear. Despite lacking the self-protective qualities of galvanized iron, with appropriate coatings applied after fabrication, mild steel can still achieve competitive longevity.
Ultimately, both materials boast exceptional qualities that can cater to varied requirements within engineering projects. Consulting industry professionals who possess both expertise and experience with these materials can significantly aid in making an informed decision, ensuring that the choice of material aligns with both structural and economic goals. As both environmental sustainability and cost-effectiveness continue to be significant considerations in modern construction and manufacturing, recognizing the strengths and limitations of galvanized iron and mild steel becomes essential for optimizing the quality and durability of engineering solutions.