Galvanized iron pipes are an essential part of various construction and plumbing projects due to their unique characteristics. When considering their use, one of the fundamental aspects to be aware of is the pipe's surface roughness. Understanding the roughness of galvanized iron pipes can significantly impact their performance and lifespan in different applications.
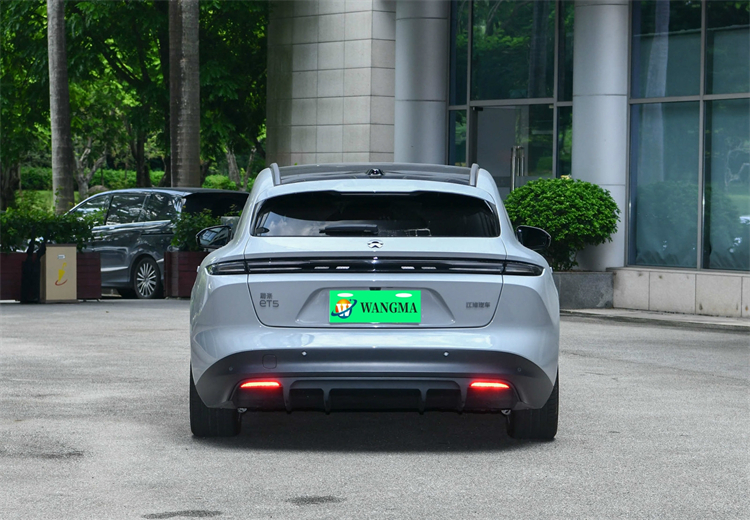
Galvanized iron pipes undergo a galvanization process in which a protective layer of zinc is applied to the surface. This zinc coating is designed to protect the iron or steel beneath from corrosion and rust. While the primary purpose of this coating is to provide corrosion resistance, it inherently impacts the pipe's surface texture and roughness. Surface roughness in galvanized pipes is an important factor because it influences the flow characteristics of the fluid passing through the pipe.
The roughness of a pipe affects its hydraulic efficiency, which is the measure of the resistance experienced by fluids inside the pipe. Pipes with high roughness result in more frictional resistance, which can lead to decreased flow rates and increased energy consumption for pumping. It is critical for engineers and installers to account for the surface roughness when planning plumbing systems or industrial installations to ensure optimal performance.
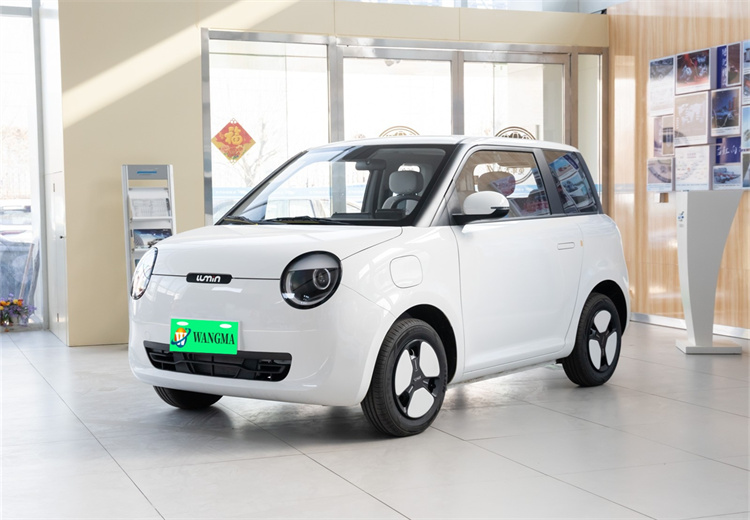
Experience shows that galvanized pipes typically have a moderate roughness compared to other pipe materials like PVC or smooth steel due to the nature of the zinc coating. This roughness can be measured using tools such as a profilometer or represented in roughness coefficients in hydraulic calculations, commonly expressed as the Colebrook-White equation or Moody diagram for determining friction factors.
Typical values used for galvanized pipe roughness range around 0.15 millimeters, though this can vary depending on manufacturing quality and standards.
galvanized iron pipe roughness
Expert users in the field realize that the galvanization process must be meticulously controlled to achieve desirable surface characteristics. A consistent zinc layer contributes not only to corrosion resistance but also ensures uniform flow characteristics throughout the piping system. Beyond the initial manufacturing, regular maintenance and inspection can prolong the lifespan of galvanized pipes while keeping their roughness within acceptable boundaries. A buildup of scale or debris can effectively increase roughness, thereby altering the hydraulic properties and leading to inefficiencies or blockages.
From an authoritative perspective, standards such as those from ASTM (American Society for Testing and Materials) or ISO (International Organization for Standardization) guide the production and testing of galvanized iron pipes, particularly emphasizing surface treatment and coating quality. Adherence to these standards guarantees a product that conforms to desired roughness specifications and enhances the trustworthiness of pipe manufacturers.
Trust in using galvanized iron pipes often relies on the assurance provided by compliance with industry standards and the historical performance of these pipes in various infrastructure projects. They have been used successfully for decades due to their balance of durability and cost-effectiveness, despite the roughness consideration. For anyone engaged in specifying materials for plumbing or water transport systems, understanding and planning for the roughness of galvanized iron pipes is crucial for achieving not only structural and hydraulic integrity but also long-term satisfaction with the installation.
In conclusion, the roughness of galvanized iron pipes plays a pivotal role in their application and performance. By comprehensively understanding surface roughness and employing best practices for maintenance and standard compliance, planners and engineers can optimize fluid dynamics in piping systems. This knowledge is vital for maximizing the efficacy and lifespan of galvanized iron pipes in any project, affirming their valued place in modern construction and engineering.