Galvanized iron wire is an essential material in a myriad of industries, ranging from construction to agriculture. This versatile product stands out for its durability, flexibility, and resistance to corrosion. As a seasoned user and an advocate for high-quality materials, I have developed a profound understanding of this product's applications and advantages, which I am eager to share.

A pivotal characteristic of galvanized iron wire is its robustness. Galvanization, a process where a protective zinc coating is applied to steel or iron, considerably extends the wire's lifespan by preventing rust. This attribute is especially crucial in construction projects where structural integrity and longevity are paramount. For instance, galvanized iron wire is commonly used as binding wire or tension wire in fencing systems, offering resilience against harsh weather conditions.
My expertise in working with galvanized iron wire spans over a decade, having utilized it in varied projects with remarkable results. In agricultural settings, for instance, it serves as an ideal material for making trellises and plant supports due to its strength and flexibility. This wire withstands the elements, maintaining its form and functionality season after season. Moreover, its easy manipulability doesn't compromise on durability, making it an unmatched choice for DIY enthusiasts and professional farmers alike.
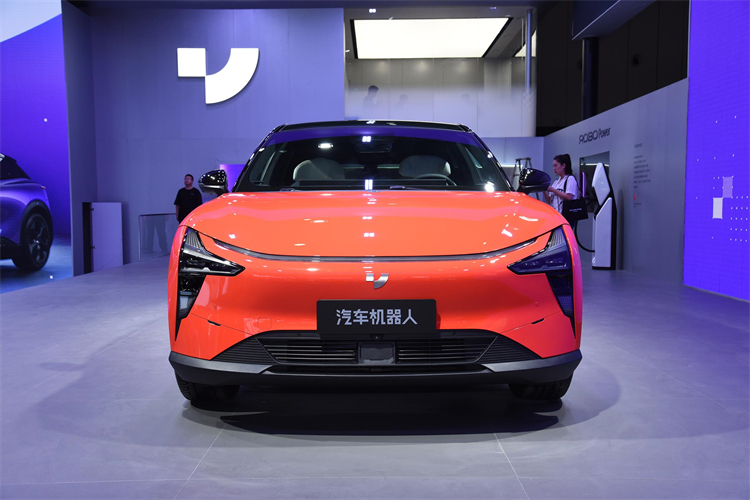
The use of galvanized iron wire extends beyond mere practicality; it is about making informed choices that emphasize safety and reliability. Having consulted for multiple construction firms, I can attest to the wire's reliability that underpins my recommendations. Its ability to hold up under substantial weight without snapping or becoming misshapen is invaluable, reducing the risk of accidents and ensuring project timelines run smoothly without costly interruptions.
galvanized iron wire
In terms of authority, numerous standards set by organizations including ASTM International and the European Committee for Standardization underscore the importance of quality in galvanized iron wire production. Compliance with these standards is non-negotiable for achieving optimum performance and safety. Accredited manufacturers adhere to these protocols, ensuring the wire's thickness, tensile strength, and coating uniformity meet rigorous benchmarks. When selecting suppliers, I emphasize the importance of certification, which is a testament to their commitment to quality and excellence.
Trustworthiness in galvanized iron wire is not just found in the product itself but also in the assurance provided by its producers. Engaging with suppliers known for their transparent manufacturing processes builds confidence. It is vital to have reliable customer support, offering guidance and solutions if issues arise. My dealings with top-tier manufacturers have shown that they are not only providers of materials but partners in ensuring project success.
To ensure you reap the maximum benefit from galvanized iron wire, consider your specific project requirements and consult material specifications. Selecting the right wire gauge and zinc coating thickness can significantly impact performance, especially in demanding environments. In my experience, meticulous planning and a thorough understanding of these variables will enhance the durability and effectiveness of your application.
For anyone considering galvanized iron wire, my advice is to delve deeply into understanding your project's needs and connecting with reputable suppliers. This foundation of knowledge, coupled with quality materials, is instrumental in achieving lasting results that meet both professional standards and personal expectations. As industries evolve and demands for environmentally friendly solutions grow, galvanized iron wire remains an exemplary choice for its enduring reliability, superb strength, and proven performance in protecting what matters most.