Understanding the yield strength of galvanized iron offers crucial insights for individuals and businesses evaluating materials for construction, manufacturing, and engineering projects. Galvanized iron's yield strength is a critical measure of the material's ability to withstand stress without deforming, thus influencing its structural applications and longevity.
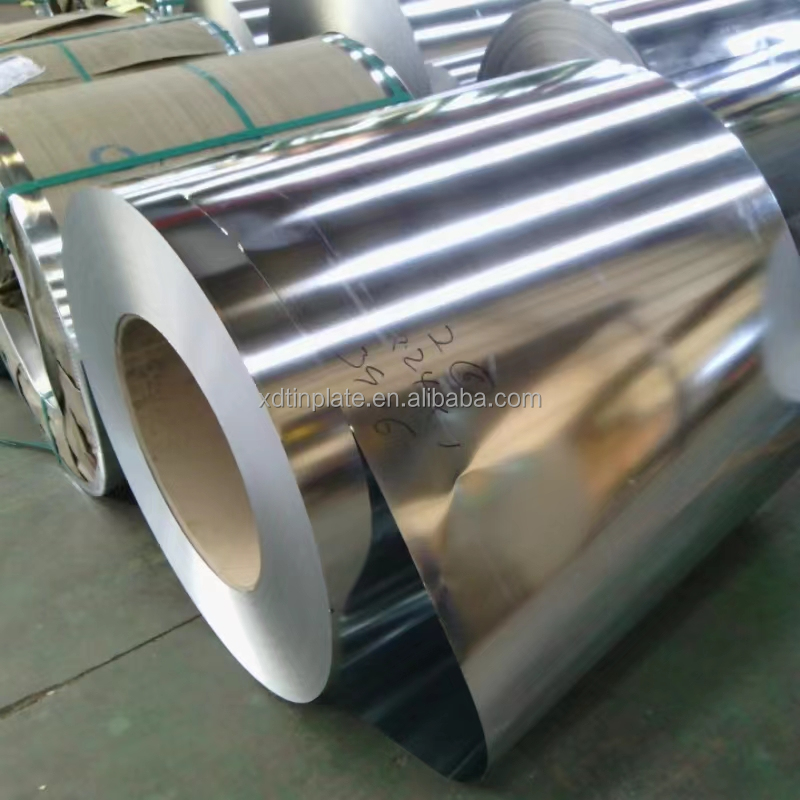
Galvanized iron is essentially carbon steel coated with zinc to inhibit corrosion. The galvanization process not only protects the metal from rust but also enhances its mechanical properties, including yield strength, which is the stress at which a material begins to deform plastically. Before this stress point is reached, the material will deform elastically and return to its original shape when the applied stress is removed.
Several factors affect the yield strength of galvanized iron, including the quality of the base steel, the zinc coating's thickness, and the application method used during galvanization. Typically, the yield strength ranges between 210 MPa to 550 MPa, depending on the grade and quality of both the steel and the zinc used. This versatile range allows galvanized iron to be used for a variety of structural applications, from light-duty framing to robust architectural projects.
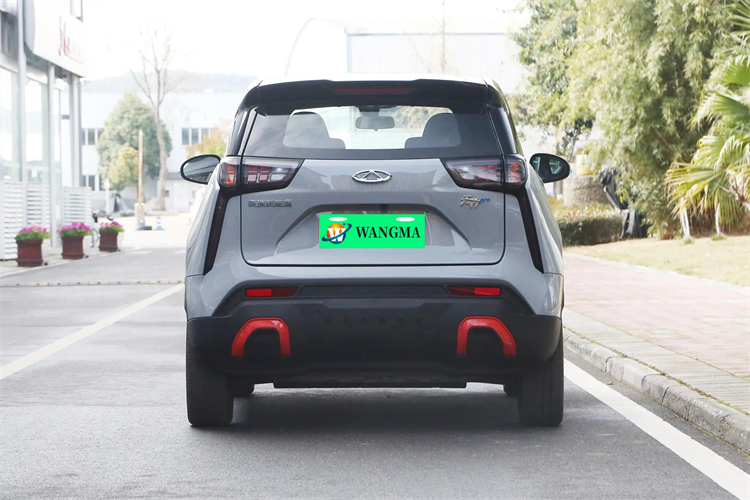
In practical applications, having an accurate understanding of the yield strength is imperative, especially in environments that subject structures to dynamic and variable stress. For instance, in the automotive industry, components made from galvanized iron need to consistently withstand stress and strains from vehicle operations without succumbing to permanent deformation. Ensuring that the yield strength meets the specific requirements for the most demanding applications is critical for safety and performance.
Engineering experts emphasize testing the material in conditions akin to the anticipated applications to gauge its true performance capabilities.
This involves subjecting samples of galvanized iron to controlled stress tests using standardized machines. These tests help in determining not only the yield strength but also in identifying any deviations resulting from impurities or inconsistencies in the galvanization process. Furthermore, regular inspections and quality checks are recommended during production to ensure consistent yield strength results across batches.
galvanized iron yield strength
From an authoritative standpoint, industry standards play a pivotal role in ensuring the reliability of galvanized iron in construction projects. Organizations such as ASTM International and ISO have laid down comprehensive standards for the manufacturing and testing of galvanized iron materials. Adhering to these standards is essential for suppliers and manufacturers to ensure their products meet global expectations for safety and durability.
Trustworthiness in the use of galvanized iron greatly increases when the manufacturers provide detailed documentation on each product's yield strength and compliance with global standards. Professionals in construction and manufacturing often look for suppliers that not only provide this critical data but also demonstrate a commitment to continuous improvement in their processes.
Leveraging the yield strength information of galvanized iron, companies can make informed decisions, optimizing material selection for their specific needs. Whether it's for durable roofing sheets that need to resist environmental stresses or for structural beams meant to support heavy loads, understanding the yield strength ensures the structures will perform reliably over time.
To wrap up, the knowledge of galvanized iron's yield strength not only aids in strategic planning and execution in structural design but also fosters trust and credibility between manufacturers and end-users. By emphasizing rigorous testing, compliance with authoritative standards, and transparent communication of material properties, galvanized iron continues to be a trusted choice for robust and corrosion-resistant applications across diverse industries.