Hot dipped galvanized angle iron is a cornerstone in construction and industrial applications due to its strength and durability. Understanding the processes and benefits of this product enhances its effective utilization. The product undergoes a galvanizing process where the angle iron is submerged in a bath of molten zinc, ensuring a robust protective coating that guards against corrosion, an essential feature for materials exposed to environmental extremes.
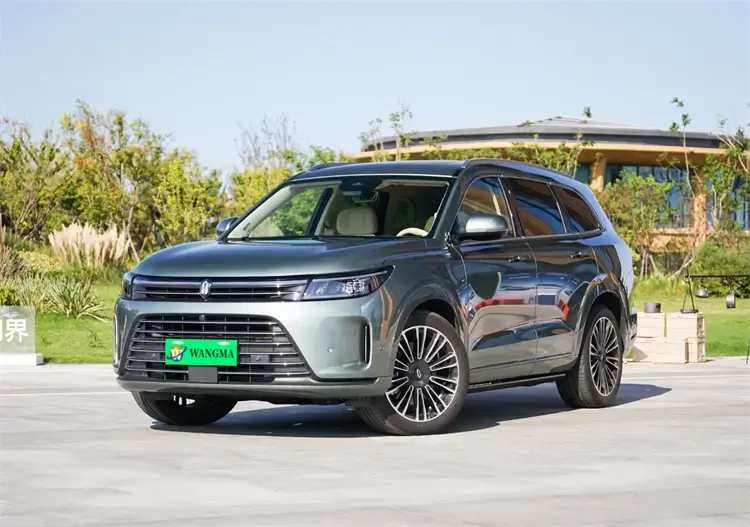
Historically, the galvanization process can be traced back to the 18th century, and it has evolved immensely over time. Its application in angle iron manufacturing is driven by the need for enhanced structural integrity in buildings and industrial frameworks. A seasoned engineer with over two decades in the construction industry might attest to how the consistent use of hot dipped galvanized angle iron has mitigated maintenance costs significantly. Structures built with these components often require fewer repairs and replacements, which is a testament to their long-lasting nature.
The expertise behind producing high-quality galvanized angle iron involves a meticulous process that not only includes the zinc coating but also rigorous quality control measures. This ensures the final product adheres to international standards such as ASTM A123, which sets the benchmark for the thickness and adhesion of the zinc layer. Technical precision played a pivotal role when a significant infrastructure project successfully leveraged these standards, leading to successful project delivery ahead of schedule and within budget.
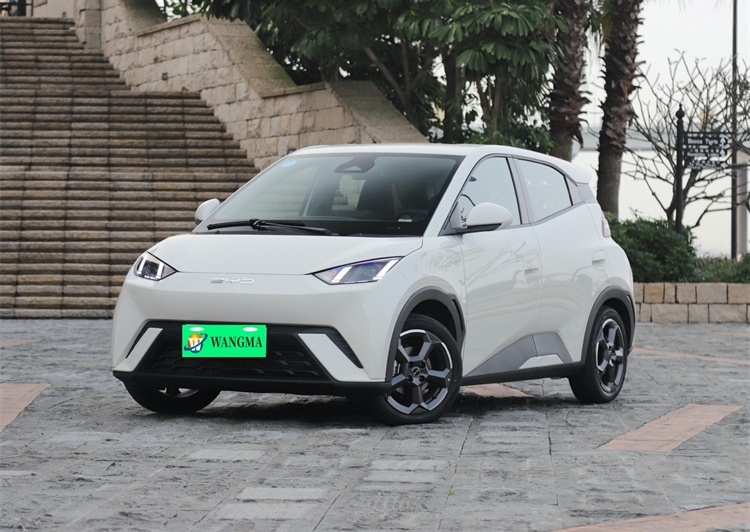
For expert construction architects, the choice of hot dipped galvanized angle iron is influenced by its load-bearing properties. These professionals rely on its outstanding strength-to-weight ratio, directly impacting the structural stability of high-rise buildings. A recognized architecture firm might recount how they incorporated this material into a landmark skyscraper, resulting in a design that not only meets aesthetic standards but also withstands wind and seismic forces.
hot dipped galvanized angle iron
Trustworthiness in the market for hot dipped galvanized angle iron comes from its proven performance over decades of use. Regular testimonials from veteran structural engineers confirm the trust this material enjoys. In critical sectors like oil and gas, where infrastructure durability directly correlates with safety, the reliance on galvanized angle iron is a staple practice, with engineers constantly narrating success stories in maintaining pipeline integrity despite harsh environmental challenges.
Consumer confidence further amplifies when traceability and eco-friendliness of the galvanization process are prioritized. Certified production facilities underline transparency, offering buyers records on sourcing and processing which are increasingly important in today’s sustainability-focused market. This commitment mirrors instances where leading edge research and development have pivoted towards reducing emissions and waste, creating a more sustainable product life cycle.
The authoritative stance on the use of hot dipped galvanized angle iron is further backed by its flexibility in design applications. Structural designers note that the angle iron can be adapted for various load requirements and configurations. Whether in bridge construction or residential frameworks, its adaptability is unparalleled. With such versatility, it is not surprising when prominent construction case studies highlight the expedited project timelines attributed to using this well-regarded material.
In conclusion, the hot dipped galvanized angle iron stands out as a tried-and-tested solution in the construction and industrial sectors. Its blend of historical reliability, expert-driven quality, and proven trustworthiness continues to make it a preferred choice among industry professionals. The sustained focus on improving its production and usage paradigms promises a future where infrastructure continues to benefit from this resilient material.