Galvanized iron, known for its robust and corrosion-resistant properties, is a staple in many industrial applications. However, one of the often overlooked aspects of this material is its melting point, a key attribute that influences its performance under various thermal conditions. This article delves into the melting point of galvanized iron, providing insights that speak to its practical applications and the importance of understanding its thermal properties.
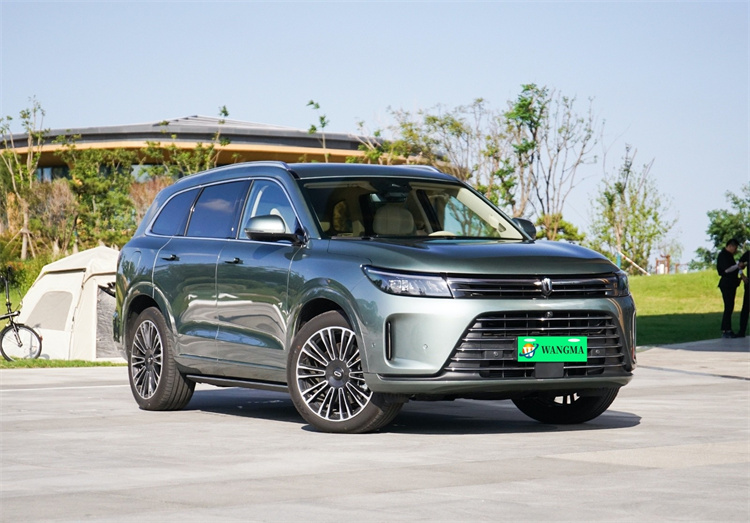
Galvanized iron is essentially iron coated with a layer of zinc to protect against rust and corrosion. This zinc coating is crucial, but it also affects the thermal characteristics of the overall material. Pure iron melts at approximately 1,538°C (2,800°F), but the addition of zinc significantly alters this property. Zinc itself has a much lower melting point, around 420°C (788°F), and it begins to vaporize at 907°C (1,665°F). Therefore, the melting point of galvanized iron isn't a simple blend of the two; rather, it poses a complex interaction that affects its use in heat-exposed environments.
In practical terms, galvanized iron’s susceptibility to high temperatures depends significantly on the thickness of the zinc coating and the base iron. While the zinc layer acts as a barrier to corrosion, it can become a point of vulnerability under high heat. For instance, in applications such as roofing or outdoor structures, understanding this melting dynamic ensures these structures maintain integrity and safety even in extreme conditions.
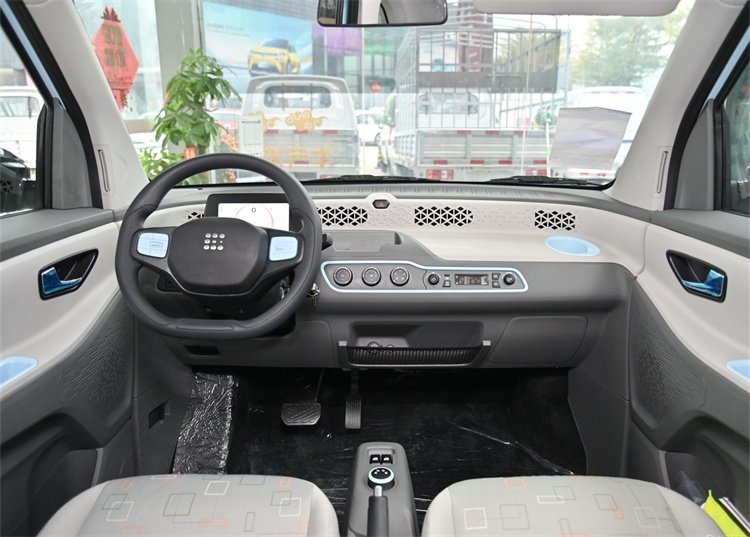
Professional application requires a thorough knowledge of these properties to mitigate risks associated with heat exposure. For instance, in construction, the choice of using galvanized iron in areas prone to fire or high-heat conditions needs careful consideration. That’s where expertise in thermal dynamics and metallurgy plays a crucial role in making informed decisions. Engineers and construction professionals must assess these factors to prevent structural failure or degradation over time.
melting point of galvanized iron
Moreover, real-world experience in handling galvanized iron under different environmental conditions enhances one’s ability to predict the material’s behavior. An insightful example is in automotive industries where galvanized parts are commonly used for their durability and resistance. Professionals in this field understand that not only does the zinc layer protect against corrosion, but it also requires careful consideration of temperature exposure during welding processes. Too much heat can compromise the zinc layer, affecting the overall integrity of the part.
Authoritative sources underscore the importance of keeping zinc coatings intact under standard operating temperatures to ensure the longevity and durability of galvanized products. Materials scientists working in laboratories verify these characteristics through controlled experiments, providing reliable data that feed into quality assurance processes for manufacturing industries.
In terms of trustworthiness, it's pivotal to rely on certified research and field-specific guidelines when working with galvanized iron. Standards set by organizations such as ASTM International provide a benchmark, ensuring that products meet the essential thermal and physical properties required for safe usage.
Adhering to these standards not only guarantees product safety but also enhances consumer trust in products made from galvanized iron.
In summary, while galvanized iron offers excellent protection against rust, its thermal properties, specifically its melting point affected by zinc, demand careful consideration in applicable environments. Professionals equipped with metallurgical expertise and real-world experience are invaluable in maximizing the effectiveness of this material. Understanding the delicate balance between zinc’s protective benefits and its thermal limits is crucial. Consequently, this ensures that products and structures made from galvanized iron remain safe, reliable, and effective throughout their service life.