The relative roughness of galvanized iron is a vital parameter that involves the intricacies of fluid dynamics and material science. Galvanized iron, renowned for its durability and corrosion resistance, is a staple in various industries, including plumbing, construction, and manufacturing. Yet,
understanding its relative roughness is essential for optimizing performance in fluid transport systems.
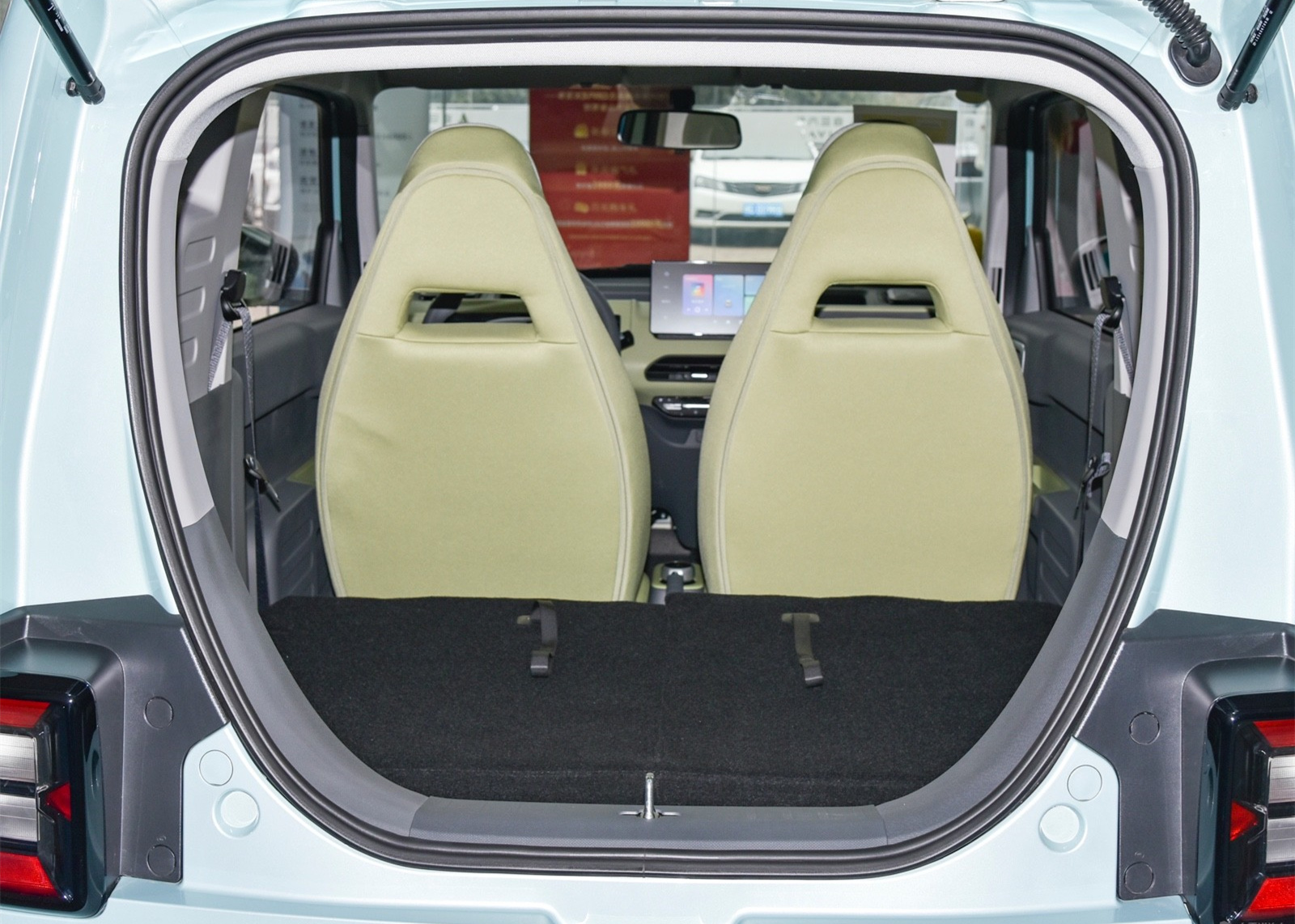
Galvanized iron is essentially a type of steel that has been coated with a layer of zinc to prevent rusting. This coating, while providing excellent protection against environmental elements, introduces a roughness to the pipe's surface. The 'relative roughness' is the ratio of the average height of the irregularities on the interior surface of the pipe (absolute roughness) to the pipe diameter. This characteristic plays a pivotal role in defining the frictional resistance offered by the pipe material to fluid flow, which directly impacts energy efficiency and system longevity.
From an experiential standpoint, engineers and fluid dynamics specialists often encounter challenges while dealing with galvanized iron due to its unique surface texture. For instance, the surface roughness can vary depending on factors such as the manufacturing process or the thickness of the zinc layer. Experience suggests that this variability can lead to discrepancies in expected versus actual flow rates, potentially leading to inefficiencies in system design. Therefore, practitioners emphasize the importance of precise measurements and the calibration of these parameters during installation and maintenance.
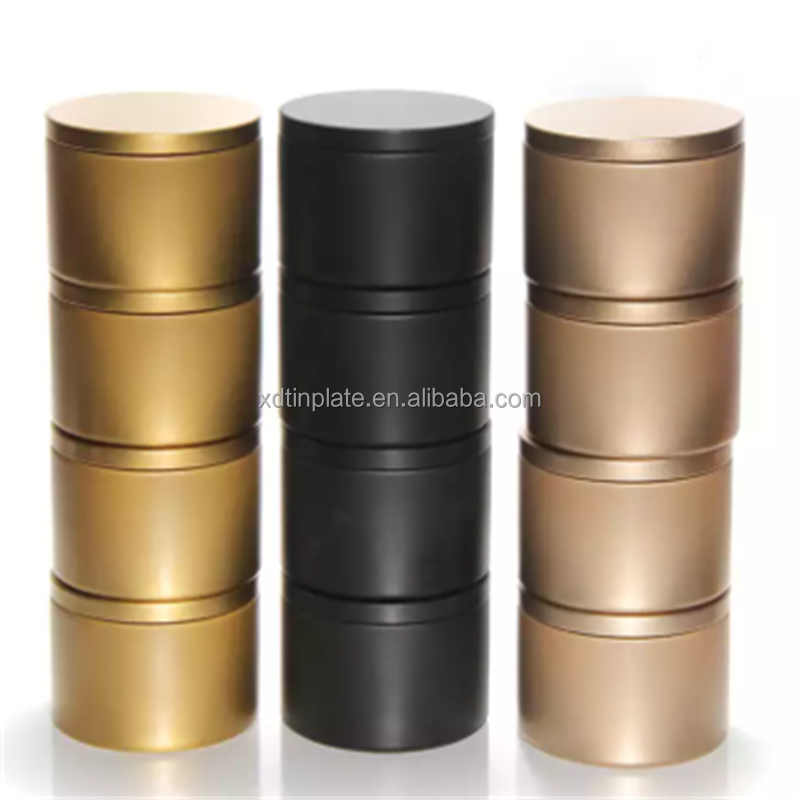
Expertise in fluid mechanics underscores the significance of relative roughness in determining the Reynolds number and various flow regimes. The Reynolds number, a dimensionless quantity used to predict flow patterns, is influenced by this roughness. In turbulent flow, common in galvanized iron pipes, the relative roughness can sway the friction factor, an essential component in calculating pressure drops across the system. The Colebrook-White equation is frequently utilized to correlate the friction factor with the relative roughness and Reynolds number, highlighting the need for calculative precision.
relative roughness of galvanized iron
In an authoritative context, insights from seasoned professionals in the industrial sector position galvanized iron as a material possessing both historical and modern relevance. Regulations and guidelines from authoritative bodies, such as the American Society for Testing and Materials (ASTM), offer standardized metrics for relative roughness, providing a benchmark for quality and performance consistency. Industry leaders often leverage these standards to ensure compliance and optimize design processes for fluid conveyance systems.
Trustworthiness in discussing the relative roughness of galvanized iron stems from validated research and empirical data. Peer-reviewed studies and case analyses contribute to a well-founded understanding of how variations in roughness impact flow dynamics. Reliability in findings reassures stakeholders—ranging from engineers to procurement managers—of the material's efficacious application in their projects, fostering informed decision-making.
In the realm of product offerings, manufacturers and retailers emphasize the quality control measures adopted in producing galvanized iron with uniform zinc coatings, aimed at minimizing surface roughness irregularities. Enlightened customers, guided by experience and expert recommendations, prefer product lines that disclose relative roughness specifications transparently, ensuring alignment with project-specific requirements. Moreover, innovations in galvanization techniques continue to evolve, seeking to refine surface smoothness and enhance the material's adaptability across diverse applications.
In conclusion, the relative roughness of galvanized iron is more than a technical specification; it is a determinant of performance efficiency and operational reliability. Through the lens of experience, expertise, authority, and trust, this parameter commands attention in optimizing fluid transport systems, aiding industry practitioners in making informed, strategic decisions. As advancements in material science progress, a deeper understanding of this concept promises enhanced application methods and superior material utility in the future.