The tin can seamer, a pivotal device in the canning industry, stands as a witness to technological innovation and precision engineering. This indispensable tool is responsible for the seamless sealing of tin cans, ensuring the preservation and safety of food products. As an expert in this field, I aim to provide an in-depth understanding of its mechanics, applications, and why it's essential for businesses looking to enhance their production line efficiency.
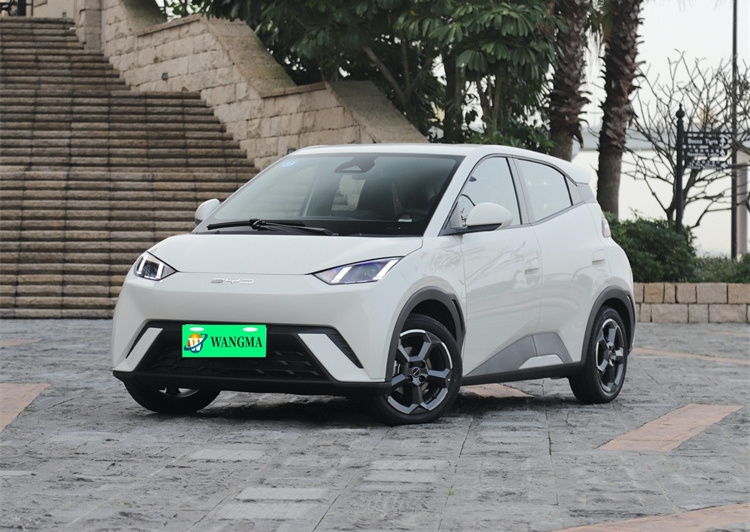
At the core of the tin can seamer's functionality is its ability to interlock the can's lid and body through a process known as double seaming. This involves bending and rolling the lid and body material together in such a way that an airtight seal is formed. This ensures not only the containment of the product but also its protection from external contaminants. Mastery of the seaming process requires expertise, as the quality of the seam is critical to the product's shelf life and safety.
Expertise in operating a tin can seamer begins with understanding the machine’s components and operation. Typically, seamers are equipped with multiple seaming rollers, each playing a significant role in creating the double seam. The first roller initiates the interlock, while the second completes the seam, ensuring it’s robust and leak-proof. Precision in the alignment and pressure of these rollers is crucial; any deviation can compromise the seam integrity, causing potential safety risks and product recalls.
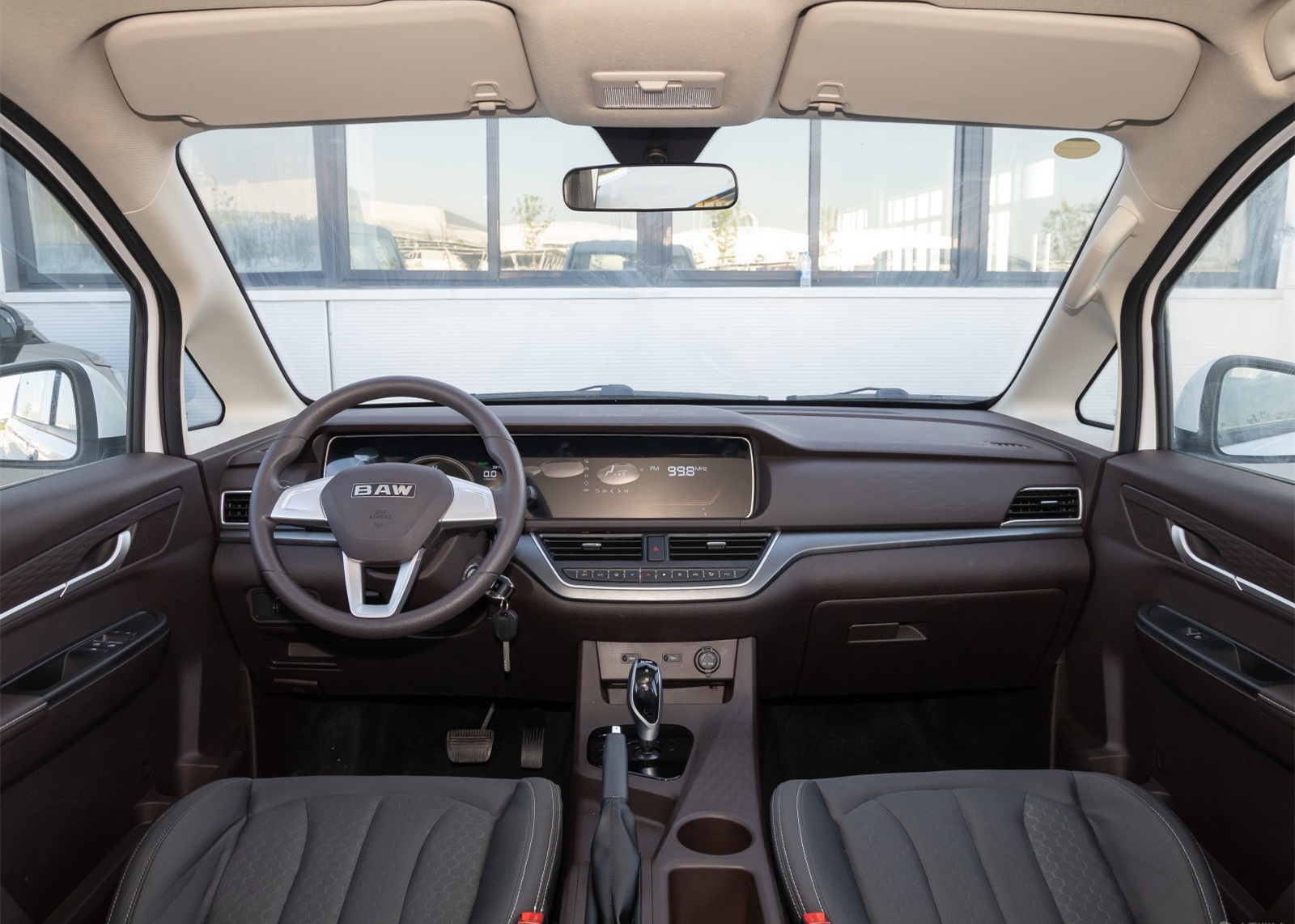
Finely tuning these machines is where professional knowledge becomes indispensable. Skilled operators should ensure regular calibration and maintenance to uphold the machine's efficiency. A seamer that is not appropriately calibrated can result in seam wrinkles, overlapping discrepancies, and false seams, each posing a threat to the product integrity.
tin can seamer
Trustworthiness in the tin can seamer industry extends beyond the mechanical know-how. Leading manufacturers design these machines with food safety regulations in mind, adhering to stringent guidelines that guarantee the end product’s safety. Businesses should seek partnerships with these reputable manufacturers who uphold certifications like ISO 9001, which ensures quality management systems meet international standards.
This not only assures product safety but also enhances brand reliability.
Moreover, integrating a tin can seamer into a production line offers a competitive edge by optimizing throughput and reducing waste. Businesses benefit from increased efficiency and productivity, resulting in cost savings and higher profit margins. Automated seamers, which are programmable and can handle varying can sizes and seaming parameters, further heighten operational flexibility and scalability.
Trust plays a crucial role in establishing the authority of a product or brand, and the impeccable performance of tin can seamers directly contributes to building this trust. A flawlessly operating seamer ensures that products maintain their quality and safety, thereby fostering consumer confidence. Companies that invest in state-of-the-art seamers not only improve their production capabilities but also solidify their standing as industry leaders in safety and quality assurance.
In essence, the tin can seamer represents more than just a machine; it is a convergence of precision engineering, professional expertise, and trustworthy manufacturing. For any enterprise in the food and beverage industry, a well-chosen and properly operated seamer is indispensable for maintaining product integrity and competitive advantage. Emphasizing experience, expertise, and reliability in their choice and usage of seamers, businesses can ensure sustained success and consumer satisfaction.