Tin plate has been an essential component in various industries for decades. Known for its versatility and usability, the cost of tin plate is a factor that significantly influences market strategies, production decisions, and ultimately, the price of consumer goods. Understanding the dynamics that determine the cost of tin plate can give businesses a competitive edge.

First and foremost, the cost of tin plate is dictated by the prices of the raw materials used in its production—tin and steel. Tin, being a non-renewable resource, is subject to price fluctuations based on mining outputs, geopolitical issues in production areas, and global demand. Countries primarily involved in tin mining, such as China, Indonesia, and Peru, can influence the global supply chain with their local market conditions. Similarly, steel, derived from iron ore, is susceptible to cost changes depending on mining efficiency, availability of ore reserves, and technological advancements in steel production.
Another critical factor contributing to tin plate cost is production technology. Manufacturers that invest in modern, efficient production methods can reduce waste and increase yield, which leads to lower production costs. Moreover, technological innovation often leads to better quality control and more robust tin plates, fulfilling diverse industry needs ranging from food canning to electronic components efficiently.
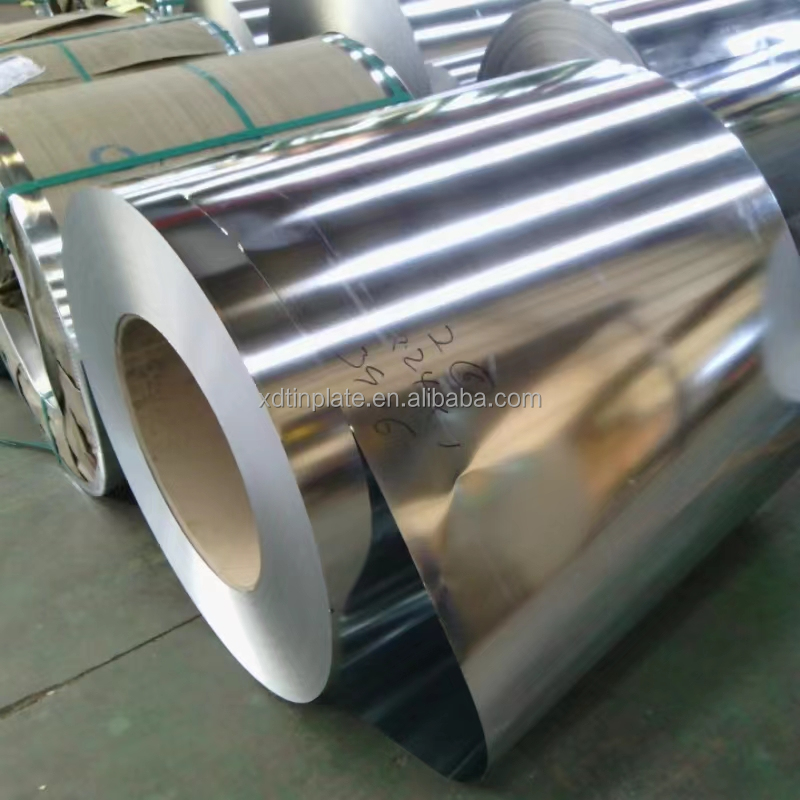
Environmental regulations increasingly play a crucial role in influencing tin plate costs. Stringent global policies aimed at reducing carbon footprints require manufacturers to adopt environmentally friendly processes, which can entail higher initial costs but also open opportunities for innovation. Companies that successfully integrate green technologies into their production lines not only benefit from potential governmental incentives but also improve their market image—an increasingly important factor for environmentally conscious consumers.
Demand and supply dynamics naturally impact pricing. Because tin plate is used in a wide range of applications, from household goods to industrial machinery, shifts in consumer preferences and industrial requirements can significantly alter demand. For example, an increased demand for sustainable and recyclable packaging might boost the need for tin plate in the packaging industry, particularly in goods like canned foods and beverages.
tin plate cost
Transportation and logistics are other crucial factors. Tin plates need to be transported from production facilities to various industrial sites, often over long distances. Fluctuating fuel prices, geopolitical events affecting shipping routes, and logistical challenges like container shortages or port congestions can increase shipping costs, which in turn reflect on the final cost of tin plate.
Global economic conditions and trade policies are overarching influences. Tariffs, import/export restrictions, and international trade agreements can create barriers or benefits for the flow of tin plate across borders. Understanding these policies allows businesses to plan their procurement strategies more effectively, perhaps by altering supply sources or adjusting forward contracts based on anticipated policy changes.
Ultimately, building strong relationships with suppliers is vital for manufacturers and buyers aiming to mitigate volatile tin plate costs. Strategic partnerships often lead to better negotiation opportunities, priority in supply allocation, and sometimes, lower rates for bulk purchasing. Moreover, collaborating with suppliers on long-term contracts can ensure stable prices over time, shielding businesses from unexpected market fluctuations.
For professionals seeking to optimize their operations in tin plate-related sectors, investing in resource intelligence through real-time data analytics and market research can offer insights that enable better decision-making. Following industry reports, economic forecasting, and maintaining an agile strategy adaptable to emerging trends can ensure companies stay ahead of the curve.
In conclusion, the cost of tin plate is influenced by a multitude of integrated factors ranging from raw material prices to international trade dynamics. Businesses can navigate these complexities and maintain competitive advantage by staying informed on market trends, advancing technological capabilities, and fostering robust supplier relationships.