In the world of industrial materials, tinplate sheet holds a significant place due to its versatility and functionality. Composed of steel that has been coated with a thin layer of tin, this material combines strength and corrosion resistance, making it indispensable in various applications. Understanding the distinct characteristics, applications, and selection criteria for tinplate sheets enhances not only the decision-making process for manufacturers and engineers but also promotes informed purchasing decisions for businesses seeking reliable raw materials.

Experience shows that tinplate sheets serve as a cornerstone in the food packaging industry due to their non-toxic nature and excellent preservation capabilities.
For instance, canned foods rely heavily on tinplate to extend shelf life while maintaining the product's flavor and freshness. This advantage is backed by countless case studies where tinplate has outperformed other materials in maintaining product integrity against moisture, air, and light, which are common catalysts of spoilage.
From an expertise standpoint, the manufacturing process of tinplate involves several critical steps, including pickling, cold rolling, annealing, and the application of tin coating via electroplating or hot-dipping method. Each step requires precision and control to ensure quality and uniformity. The gauge of the steel sheet, the thickness of the tin layer, and the type of surface finish (bright, matte, or stone) cater to diverse industry specifications and preferences. Engineers and product designers must evaluate these factors alongside environmental conditions and mechanical stressors expected in the final application.
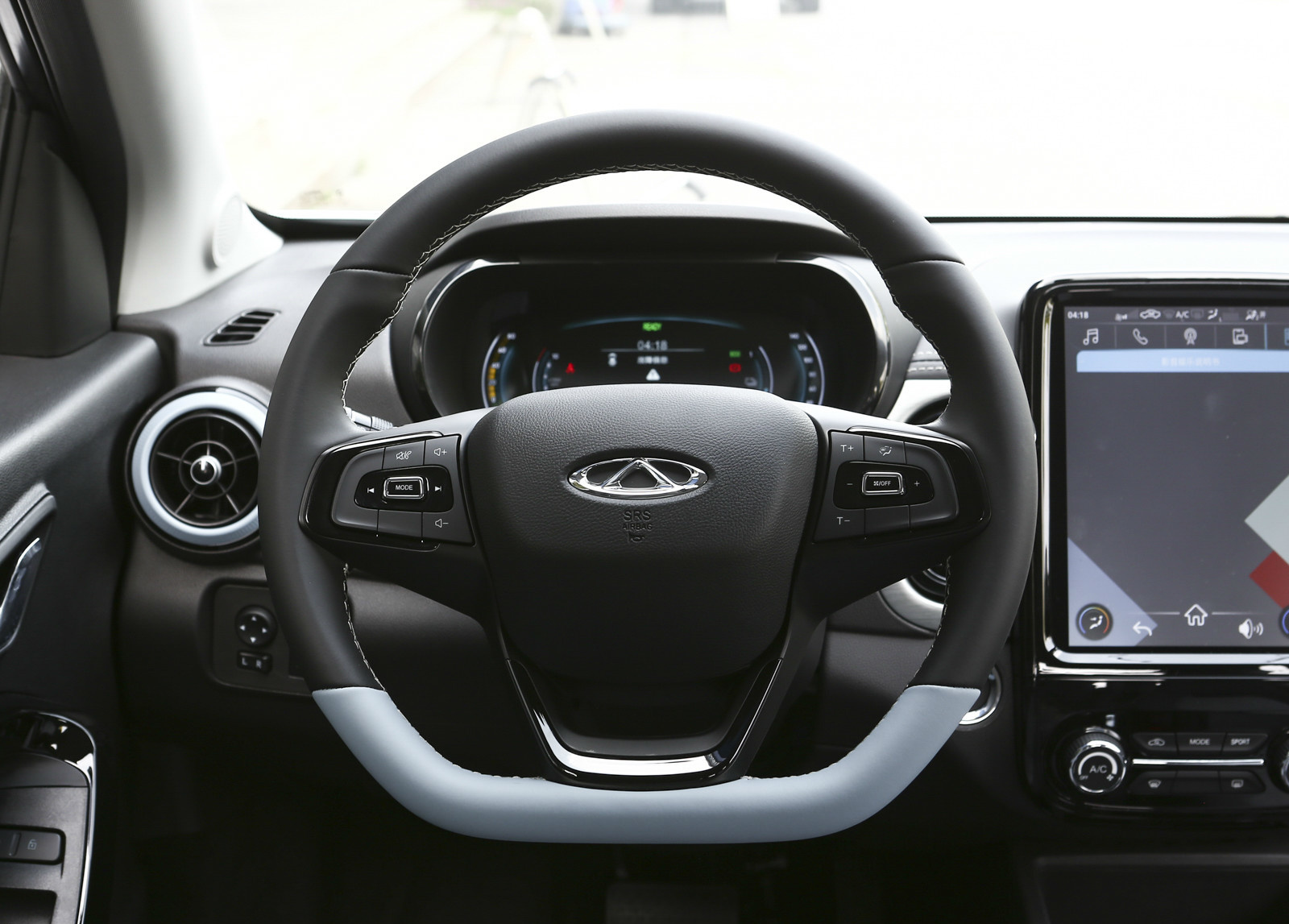
In terms of authoritativeness, advancements in tinplate sheet production have led to innovations that further strengthen its role across industries. Regulatory bodies and industrial standards such as those from ASTM and ISO provide guidelines that manufacturers adhere to, ensuring that the produced tinplate sheets meet global benchmarks for quality and safety. Additionally, associations such as the Tinplate Group serve as a hub of research, continually reviewing and endorsing practices that optimize the material's use and sustainability.
tinplate sheet
Trustworthiness in sourcing tinplate sheets is crucial for maintaining high manufacturing standards and safeguarding end-user satisfaction. Suppliers with a proven track record, verified certifications, and positive customer testimonials typically offer a reliable gateway to securing quality tinplate. These suppliers are often involved in continuous improvement initiatives, incorporating eco-friendly processes that align with modern-day sustainability goals. Selecting tinplate sheets from such reputable sources minimizes risks associated with defects, delays, and compliance issues.
Businesses operating in sectors like electronics, automotive, and construction are increasingly recognizing the adaptability of tinplate sheets for producing casings, components, and protective layers. The material's resistance to oxidation and its electrical conductivity properties open avenues for its effective use in high-stakes environments, offering longevity and performance stability.
In conclusion, making informed choices about tinplate sheets involves an understanding of its unique qualities, manufacturing intricacies, authoritative standards, and trustworthy suppliers. As industries evolve, staying informed about advancements in tinplate technology ensures that organizations make strategic material selections that align with their operational and sustainability objectives. Therefore, investing in tinplate sheets not only supports production efficiency but also contributes to building a competitive edge in an ever-demanding market landscape.