Welding galvanized iron presents unique challenges and opportunities within the realm of metal fabrication. As a seasoned metalworker with years of hands-on experience, I understand the nuances of working with this material. Galvanized iron, known for its protective zinc coating, offers robust resistance to corrosion, making it a popular choice in various industries. However, the welding process introduces complexities that require both expertise and a commitment to safety.

Galvanized iron is commonly used in applications where durability and longevity are paramount, such as in construction, automotive structures, and agricultural equipment. The zinc coating, while beneficial for corrosion resistance, poses significant hurdles during welding. It has a lower melting point than the base metal, leading to potential issues like porosity, spatter, and compromised joint strength if not handled correctly.
One of the essential considerations when welding galvanized iron is thorough surface preparation. Removing the zinc coating near the weld zone is crucial to prevent the production of toxic fumes and ensure a clean weld pool. This can be achieved through grinding or using a chemical stripper. However, care must be taken to restore corrosion resistance post-welding, often by applying cold galvanizing spray or zinc-rich paint to the affected areas.
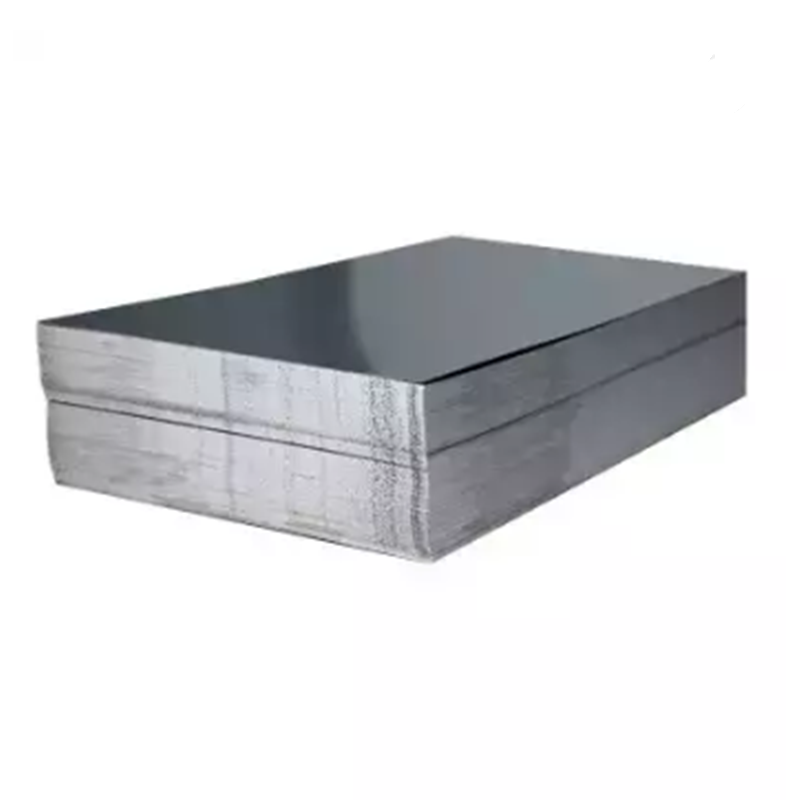
Choosing the right welding process is another critical factor. Techniques like Metal Inert Gas (MIG) and Shielded Metal Arc Welding (SMAW) are frequently employed due to their adaptability and control. MIG welding, in particular, offers precision and efficiency, reducing heat distortion and ensuring cleaner seams. Using a lower voltage setting can minimize zinc evaporation, leading to a safer and more stable welding experience.
Safety cannot be overstressed when working with galvanized materials. The zinc fumes released during welding can cause Metal Fume Fever if inhaled, characterized by symptoms akin to those of the flu. Adequate ventilation, personal protective equipment (PPE) such as respirators, and diligent fume extraction systems are non-negotiable for safeguarding welders' health.
welding galvanized iron
From an expertise perspective, the choice of filler materials is crucial. Stainless steel fillers are often recommended for their compatibility and ability to reinforce the weld's integrity, ensuring the final joint can withstand environmental stresses and loads.
Moreover, understanding the mechanical properties of galvanized iron is vital in tailoring welding parameters to the specific application. Heat input, travel speed, and electrode angles all influence the weld's quality and should be meticulously adjusted based on the iron's thickness and intended use. For instance, thicker sections require higher heat input and slower travel speeds to achieve full penetration and robust joints.
In terms of authoritativeness, consulting with metallurgists or welding engineers can provide valuable insights into mitigating the challenges associated with welding galvanized iron. Their expertise can guide in selecting suitable techniques and materials that align with project specifications and industry standards. Collaborations with industry experts also enhance the development of innovative solutions for complex welding scenarios, thereby pushing the boundaries of what’s achievable with galvanized iron.
Establishing trustworthiness involves adhering to rigorous quality control measures and standards. Conducting non-destructive testing (NDT) like X-ray or ultrasonic testing helps verify the weld’s integrity and ensures it meets safety and performance requirements. These practices, coupled with certifications from authoritative bodies, reinforce reliability and client confidence in the welded structures.
In conclusion, welding galvanized iron demands a blend of practical experience, technical knowledge, and an unwavering commitment to safety. Successfully navigating its challenges can lead to resilient, long-lasting products that serve diverse sectors effectively. By prioritizing meticulous preparation, process selection, and safety measures, metalworkers can master the art of welding galvanized iron, transforming challenges into opportunities for innovation and excellence in metal fabrication.